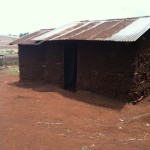
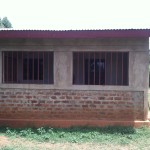
As time marches on, also the wheels of human development continue to turn. Human beings, despite their differences in geography, race, traditions, and ideology, all share something in common: a deeper longing and desire to improve and better ourselves as one race–the human race.
Evidence of our evolution (in terms of constant growth) is visible everywhere: skyscrapers, technological advancement, scientific discoveries. This modernization, particularly over recent decades, is mind-blowing. As we celebrate all these great successes in knowledge and industry, let us celebrate the seemingly humble brick-making industry in the developing villages of Africa, especially here in Kenya. Indeed, here it is a great leap of evolution to see how many families in villages are moving from mud houses into permanent brick houses.
For about the last twenty years, brick making has been viewed as one of most rapidly-growing industries in Kenya. In fact, it is one of the most reliable sources of income to many families who own infertile and agriculturally-defective lands. It is also a source of self-employment for folks with little or no formal education. There are two main catalysts for this growth: the emergence of a middle class, which is driving the demand for better and more permanent houses; and a shortage of employment opportunities among young people.
In its early stages, brick-making was viewed by many educated people as an occupation for poor and illiterate folks. But with time, and the reality of the scarcity of job opportunities, this perception has undergone a dramatic metamorphosis. Shortage of employment opportunities in the big cities and towns has forced many educated and strong young people to return to their villages and venture into the brick making industry, therefore utilizing their infertile and unproductive lands.
In comparison to agricultural use of land, one advantage of brick-making is that it can be undertaken at any season of the year. However, many brick makers prefer to fire their bricks during dry seasons, as finding dry wood during a rainy season can be challenging.
Materials required for brick making are easily obtainable, as they are natural resources:
- Clay or loam soil
- Laborers (5 men can make 1000 bricks)
- Dry wood (4,000 KSH–approximately $40–can make 5000 bricks)
- Water
- Brick-shaping box
The process of brick making:
Digging the soil, crushing, and mixing soil and water. This takes about two weeks’ time.
Molding, laying and drying, takes about one week in dry season.
Cooking of the bricks takes one full day and night. In the photos, you can see that the bricks are stacked and covered with mud to create their own insulated oven. During the dry season, when brick-firing is most common, you will see many columns of smoke continually rising over rural places; at night, the bonfire rising from the heart of the brick pile is truly beautiful.
Final examination and stacking/packaging of the bricks is the last phase of brick-making
At last the bricks are very much ready for marketing and building. During dry seasons, one brick will be sold for 5 KSH, while in rainy seasons the price will go up to 7 KSH. The brick-making industry has transformed thousand of lives in many of the villages of Kenya. It has placed food on the table, provided clothes for many families, educated many children and above all restored the usefulness of the infertile and unproductive lands.